Rozhovor: Jak se dělá vypínač - díl 2. - KONSTRUKTÉR nástrojů
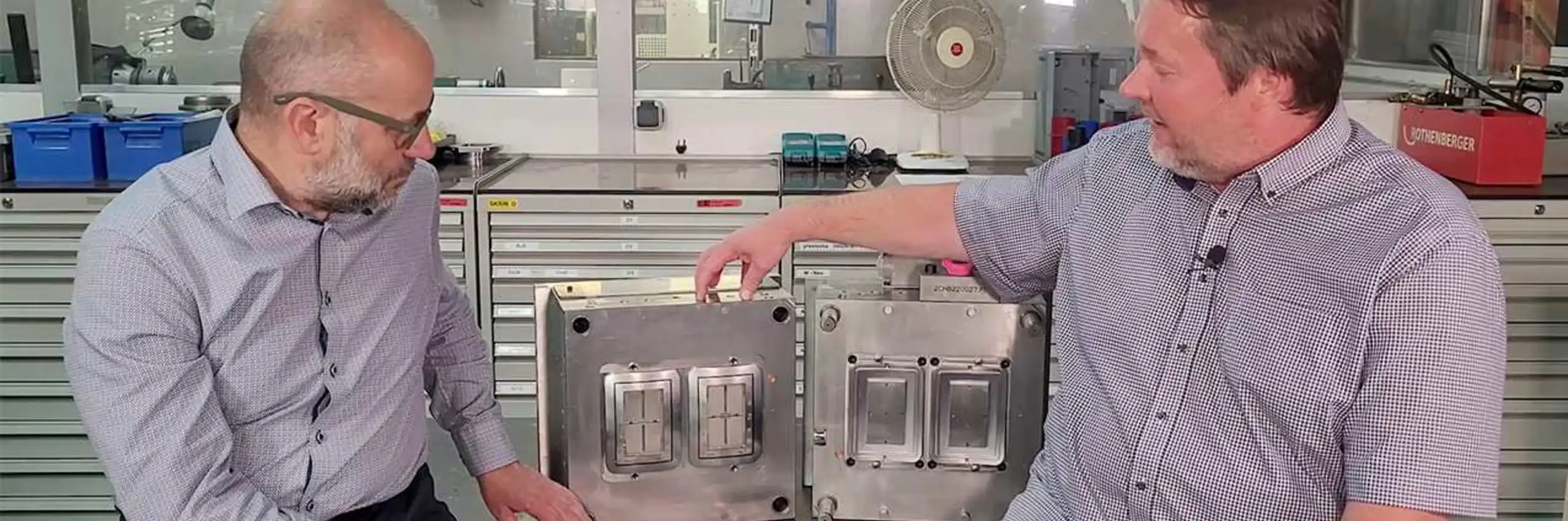
Jak dlouho v ABB pracuješ a co jsi dělal před tím?
V ABB (dříve Elektro-Praga) pracuji přes 25 let, z toho 9 let jako konstruktér nástrojů, 10 let jako vedoucí konstrukce a 7 let coby vedoucí konstrukce a výroby nástrojů.
Před příchodem do ABB jsem pracoval v Preciose jako konstruktér strojů pro opracování šatonů (skleněných broušených kamenů), následně pak ve firmě SkloPan Liberec jako konstruktér strojů, manipulátorů a automatických linek na opracování plochého skla.
Co všechno zahrnuje práce konstruktéra při výrobě vypínačů a zásuvek?
Každý takový výrobek
se skládá z kovových a plastových dílů. Konstruktér nástrojů se snaží upravit výsledný tvar těchto dílů tak, aby forma či případně nástroj šly snadno
vyrobit. Vše ladí společně s našimi designéry. V dalších krocích
navrhne koncepci formy/nástroje, vše do detailu zkonstruuje a udělá výrobní
dokumentaci.
Pak přijdou na řadu programátoři CNC strojů, kteří vytvoří potřebné programy jak pro obrábění vlastních ocelových dílů, tak elektrod pro tak zvané elektrojiskrové obrábění. Při něm se materiál odebírá drobnými elektrickými výboji mezi obrobkem a elektrodou. Následně můžeme spustit vlastní výrobu formy nebo nástroje. Výstupem práce konstruktéra tedy je, zjednodušeně řečeno, výrobní dokumentace pro danou formu nebo daný nástroj.
Nástrojaři pak jednotlivé díly nástroje vyrobí. Na konci celého procesu je potom nástrojař–mechanik, který všechny vyrobené díly seskládá dohromady, podobně jako stavebnici a sestaví z nich požadovaný nástroj.
Říkáš „výroba nástrojů“. Co je to za nástroje?
Vyrábíme tu v podstatě dva typy nástrojů. Jednomu nástroji se říká forma a slouží k lisování plastových dílů. Formu si člověk může představit jako kostku složenou z několika ocelových desek. My ty desky různě obrábíme, až z toho vznikne požadovaný tvar. Druhým typem nástrojů jsou zařízení pro tvarování kovových dílů. Opět si je můžete představit jako krabice složené z různých desek, pružinek, vedení a razníků.
Obr. Forma na lisování plastových částí vypínače nebo zásuvky (vlevo s vyhazovacím mechanizmem, vpravo statická)
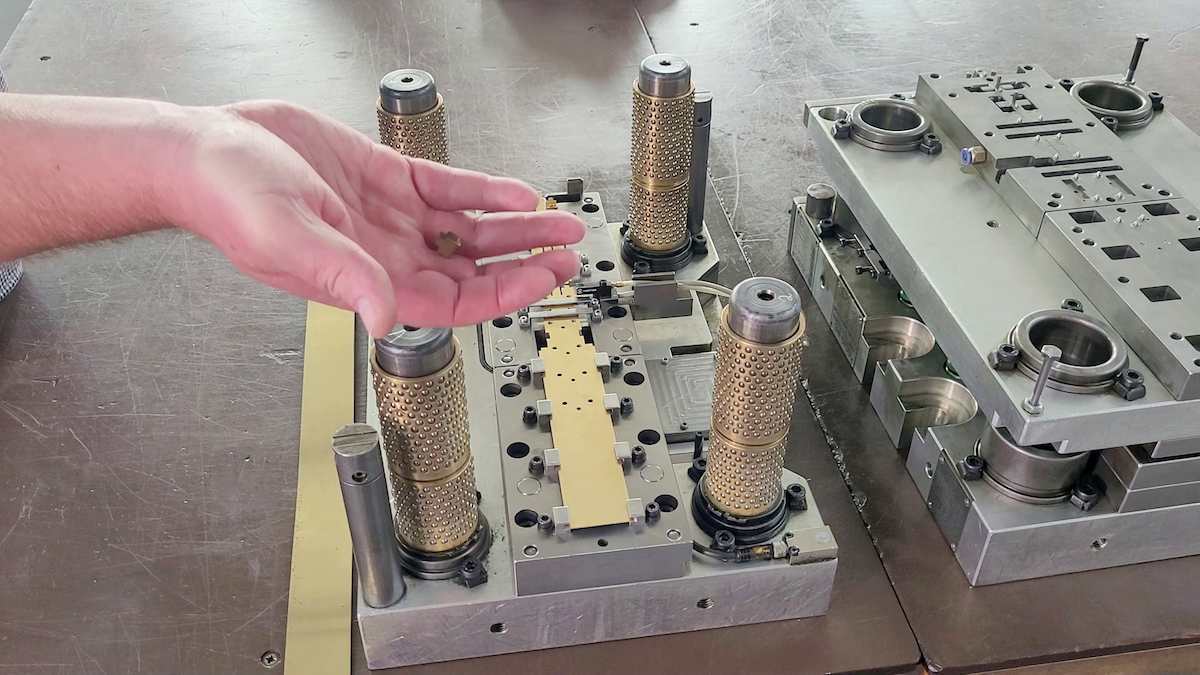
Obr. Nástroj na výrobu kontaktů pro elektrickou zásuvku<-p>
Co je zadáním pro tvoji práci? Má konstruktér při své práci prostor pro kreativitu?
Jedním vstupem je 3D model daného dílu z R&D, dále údaje od technologů lisoven plastů a kovů, na který lis má být forma nebo nástroj určen a v jaké násobnosti (tj. kolik kusů „vypadne“ při jednom zdvihu z jedné formy / nástroje). Plus další informace nezbytné ke zhotovení koncepce. Všechny tyto údaje jsou součástí tzv. „požadavkového listu“ nástroje nebo formy.
Dalším vstupem je lety vyvinutá koncepce forem a nástrojů, a vzorová 3D parametrická šablona formy/nástroje. To jsou konkrétní požadavky a postupy, které může mít každá výrobní firma trochu jiné.
Jinak ale práce konstruktéra je už ze své podstaty velmi kreativní – pokaždé se přece konstruuje něco nového. Ovšem prostor pro kreativitu má samozřejmě své hranice. Konstruktér musí dodržovat určitá pravidla hry, aby v případě potřeby mohli v rozdělané práci pokračovat jeho kolegové a bez problému věděli, co zbývá udělat a jak. Musí dodržovat pokyny, nebo chcete-li, pravidla jednotlivých zadavatelů a musí znát a respektovat možnosti technologií, které se pro obrábění dílů používají, stejně jako možnosti jednotlivých materiálů, ze kterých se forma či nástroj skládají (jak jsou pružné, pevné, odolné vůči teplu apod.)
Jak vidíte, konstruktér toho musí znát opravdu hodně, a to je na jeho práci to zajímavé.
Děláte si formy a nástroje úplně sami?
Ještě tak před 30 lety si naše nástrojárna dělala všechno sama. Od nákupu ocelových desek, z nichž se vyřezávaly autogenem polotovary jednotlivých desek rámu forem a nástrojů, až po výrobu vodicích kolíků či pouzder, vyhazovačů a dalších potřebných dílů, kterým tady u nás říkáme „bižuterie“. Výroba formy v té době trvala i s konstrukcí 10 a více měsíců, výroba složitějších nástrojů si někdy vyžádala i více než 2 roky.
Dnes už je to jiné. Postupem času vznikly firmy, které se specializují na výrobu polotovarů a komponentů pro formu. V nástrojárně se tak můžeme soustředit hlavně na precizní zhotovení tvarových částí formy a úpravu nakoupených polotovarů. Díky konstrukčnímu 3D softwaru a CNC technologiím se zkrátila doba realizace na průměrných 10 - 12 týdnů (dle složitosti formy). Díly do tzv. univerzálních rámů je díky tomu možné stihnout – ve výjimečných případech - i s konstrukcí za 4 týdny.
Kolika úpravami projde forma, než je hotová?
Díky 3D konstrukčnímu softwaru a maximálnímu využití CNC technologií dochází k hloupým chybám minimálně. V této souvislosti bych chtěl zmínit jednu věc. I když víme, co chceme zkonstruovat a vyrobit, jde téměř vždycky o prototyp. Dvě zcela identické formy/nástroje prakticky neexistují. Po sestavení jde forma či nástroj na test. Někdy je zkušební technik s funkcí formy/nástroje spokojen hned při prvním testu. Obvykle je to ale tak, že při prvním testu získáme díl, který si mohou kolegové v R&D odzkoušet, a nástrojárna před druhým testem na základě získaných zkušeností funkci formy či nástroje upraví a vylepší.
Jsou i situace, kdy se všichni začneme dost potit. Nejčastěji ve chvíli, kdy máme problémy s otevřením formy a vyjmutím vylisovaného dílu. Jinými slovy zjistíme, že díl je sice v pořádku, ale nelze ho bez poškození vyndat z dutiny formy, anebo se díl vozí na nějakém šíbru* a nelze ho manipulá-torem odebrat. V takových případech je potřeba nenechat se znervóznit požadavky na co nejrychlejší zahájení výroby a v klidu začít problém řešit. V té chvíli je také dobré zapojit konstruktéra, který na projektu nepracoval a dovede se navěc podívat s nadhledem. Ještě se nestalo, že bychom nenašli vhodnou konstrukční úpravu a problém nevyřešili.
Pozn. *) Šíbr je speciální mechanická součástka ve formě, která se pohybuje v závislosti na otevírání formy, ale obvykle v jiném směru, než je otevírání formy. Šíbr slouží k odformování např. zobáčků, nebo bočních děr, které jsou v jiném směru, než je směr otevírání formy. Představte si klasickou bábovičku z písku. Bábovička z písku v sobě nemá žádný otvor, ale pokud bychom do ní chtěli mít z boku díru, tak musíme vzít tyčinku a píchnout do bábovičky z boku. Té tyčince říkáme šíbr.
Jak probíhá spolupráce s designéry? Je těžké splnit jejich představy?
Konstruktéři a designéři spolupracují už od počátku vývoje dílu. Konkrétně v jabloneckém ABB máme tu výhodu, že konstruktéři s designéry pracují ve stejném softwaru, takže mohou velmi úzce spolupracovat na vyladění tvaru dílu a společně dojít k výsledku, se kterým jsou všichni spokojeni.
A co se týká představ designérů? Když designéři přijdou s opravdu hodně futuristickým nápadem, dostanou od konstruktérů forem klasicky odpověď, že se asi pomátli. Ale pak začneme diskutovat, někdy se i hádáme, upravujeme, zjednodušujeme, testujeme možnosti obráběcích technologií… Pak se zkonstruuje a vyrobí prototypová forma a najednou to jde, najednou je to tady a původně futuristický nápad se stává realitou! Takže ano, někdy je těžké plnit představy designérů, ale je to napínavá a zajímavá práce.
A kdybys měl srovnat práci nástrojaře před 20 lety a teď? Když jste před 25 lety pracovali na řadě Tango, tak to asi probíhalo jinak, než v současnosti třeba na řadě Levit?
Rozdíl tu je a zároveň není. Pořád je potřeba fortel a šikovnost, pořád se musí u práce myslet. Obdivuji, že předchůdci s tehdy dostupnými technologiemi uměli dosáhnout tak dobrých výsledků, např. jak pouze z běžného výkresu bez 3D zobrazování dokázali tvarově složitou dutinu bezchybně sesadit tak, aby nikde nezastřikovalo a díl byl tvarově a funkčně v pořádku. Tenkrát se jednalo převážně o ruční práci. V té době nástrojař byl v podstatě posledním designérem dílu, tvar výrobku byl ve finále podle něho.
Dnes mají nástrojaři možnost nastudovat si tvarovou dutinu, případně celou formu, na tzv. datovém kiosku ve 3D. Vědí tak zcela přesně, jak má dutina vypadat. Musím, připustit že zároveň to trochu degraduje jejich představivost. Na druhou stranu i designéři díky 3D tvoří někdy velmi náročné tvary, takže v tomhle ohledu se nároky zvyšují. Navíc je dnes obrovský tlak na rychlost zpracování. Výhodou je, že díly už není potřeba v tak velké míře jako dřív ručně dolaďovat a bonusem je to, že provoz je tak čistý, že by se dalo z podlahy jíst.
Kolik forem je potřeba na výrobu jednoho kompletního vypínače?
Když si jako příklad vezmeme základní bezšroubový spínač řady TANGO, tak je potřeba 7 forem a 4 nástroje.
Po konstrukci a výrobě formy přichází lisování. Co je na něm nejobtížnější?
Nejsložitější je udržet vše v nastavených standardech. Není to jednoduché, protože vše se vám pod rukama více či méně mění. U plastů proces lisování ovlivňují různé faktory – např. opotřebení vodících a mechanických prvků formy, čistota tvarové dutiny, průchodnosti odvzdušnění, dostatečná průchodnosti temperačních kanálů formy, správná činnosti termoregulačních zařízení a horkých rozvodů taveniny, opotřebení vstřikovací jednotky lisu atd. Je toho prostě hodně. Když se nedaří díl správně vylisovat, je někdy těžké najít příčinu. Obvykle není jen jedna, ale kombinace několika.
Jak často je potřeba formu vyměnit, po jaké době se opotřebuje?
U mechanicky středně složitých forem se počítá s životností 1 milión zdvihů (zdvih je otevření a zavření formy na lise). Jsou formy, které při správné údržbě zvládnou 2 milióny zdvihů i více. Zjednodušeně řečeno, forma vám může žít nějakých 10 až 15 let.
Vedle výroby forem a nástrojů pro nový design se tedy určitě staráte o údržbu těch stávajících. Co všechno to obnáší?
V současné době máme cca 1 750 forem a cca 330 nástrojů, které vyžadují neustálou péči a kontrolu. Na každé formě provádíme pravidelnou údržbu, což zabírá zhruba polovinu kapacity naší nástrojárny. U tzv. VIP forem (very important parts) děláme údržbu po každé „zakázce“. Velikost zakázky je nastavena tak, aby údržba byla co nejúčinnější a díly byly v co nejlepší kvalitě. To je důležité jak pro vlastní funkci dílů ve finální sestavě, tak pro potřeby automatických montážních linek. Formy nemůžeme opravovat donekonečna. V určitém stupni opotřebení už je pro nás oprava neekonomická, a tak formu vyřadíme a nahradíme novou. U nástrojů většinou stačí měnit opotřebované komponenty – nástroje jsou tak prakticky nesmrtelné.
Princip a proces výroby formy je v řadě odvětví asi podobný. Jsou u vypínačů a zásuvek nějaká specifika
Osobně mám zkušenosti jen s domovními elektroinstalačními díly, průmyslovými zásuvkami a vidlicemi, jističi a proudovými chrániči a s příchytkami pro automobilový průmysl. Ale podle toho, co jsem se dozvěděl od kolegů z ostatních ABB jednotek po Evropě, bych řekl, že žádné výrazné odlišnosti nejsou.
Co pro tebe znamená práce v ABB?
Za prvé je to pro mě způsob obživy, i když se to může někomu zdát přízemní. Za druhé mi práce v ABB umožňuje zapojit se do zajímavých projektů, kde mohu uplatnit, co jsem se za svůj život naučil. A také se naučit něco nového a profesně neustále růst. K tomu navíc v příjemném pracovní prostředí, kde vládnou skutečně dobré pracovní i osobní vztahy.
Nelákalo by tě pracovat na konstrukci i něčeho jiného, než jsou vypínače a zásuvky?
Lákalo, ale to už v tomhle životě nestihnu.

Zajímavých oborů, kde je konstrukční práce potřeba, je nekonečně. Ke všem je ale nutné v průběhu profesního života nasát know-how a to trvá roky. O tom, čemu se konstruktér v průběhu svého života nakonec věnuje, většinou rozhodují náhody.
Děkuji za rozhovor.
Rozhovor si také můžete pustit ve videu.